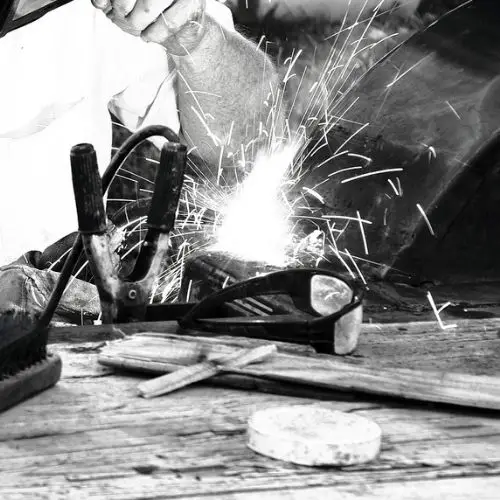
Your circuit’s polarity is essential in determining your weld’s quality and it affects your welding arc control. Choosing the incorrect polarity can cause inadequate penetration and lots of splatter and irregular bread shapes, so welders should ensure that they know the correct polarity when performing a weld.
Polarity is the electrical circuit created between a welder’s positive and negative poles when they turn on their welder. Welding polarities include electrode positive polarity or DCEP and DCEN or electrode negative polarity. DC or Direct current flows in one direction while AC or Alternating Current flows in sine wave patterns of alternating polarity.
Although these terms may seem technical, they are quite simple once you understand their workings and functions. Each polarity suits a particular style of metal and each welding process, so it is essential to master the basics to achieve quality welds. If you would like to understand how polarity works in the welding process, please read on.
How Do AC and DC Affect the Welding Process?
Contents
AC and DC welds use different currents to produce their electrical arc. Both AC and DC involve creating an arc between the electrode and the metal workpiece and provides the heat necessary to fuse the metals. The AC or DC power supply supplies the current polarity that runs through the electrode and affects the created weld.
Direct current flows only in one direction and provides constant polarity, whether it is negative or positive. Alternating Current alternates the direction of flow in high-speed alternation and thus can be regarded as an alternating current flow.
DC is mainly used in shielded metal arc welding because it has a more straightforward arc strike and results in a more stable arc performance. DC reduces the occurrence of splatter and aids in vertical up and overhead welding.
Some say that AC is commonly used for welding aluminum, but I think it’s more the case with TIG welding where AC helps to clean oxide from the metal surface.
In the case of stick welding, AC is often used for welding magnetized surfaces or when your machine does not have DC capabilities.
There are three kinds of polarity in the welding process, and each has its limitations and benefits, which are as follows.
Direct Current Electrode Negative (DCEN) Polarity
When the electrode connects to the negative terminal and the base plates are connected to the positive, it is called Direct Current Electrode Negative (or straight polarity.) The electrons flow from the electrode to the base plates with the heat concentrated in the base plate.
Because a lot of the heat is concentrated on the base plate (roughly 2/3rds) and not in the electrode itself, the electrode’s deposition rate decreases, making a smoother and more stable weld. However, DCEN may prone to inclusion defects if welders do not clean the base metal correctly.
However, as the name “straight polarity” indicates, it is the preferred polarity when stick welding. In some cases, it is not possible to use DCEN – for example when you are using 7018 rods that are only for DCEP. All-position 7018 can be used with AC current as well, but never on DCEN settings.
DCEN Advantages
- The increased heat of the base metal aids proper penetration of the weld. The DCEN process is suited to metals with high melting points such as stainless steel and titanium and lends itself to the welding of thicker plates due to its enhanced penetrative capacities.
- DCEN lessens the deposition rate of the filler metal.
DCEN Disadvantages
- DCEN does not offer the arc cleaning action of DCEP, so there is a chance that there may be inclusion defects.
- Because there is a broader heat affected area and lowered deposition rate DCEN is not suited to weld thinner plates
- DCEN has high distortion levels and generates a high level of residual stress.
Direct Current Electrode Positive (DCEP) Polarity
DCEP or reverse polarity occurs when the electrode is connected to the positive terminal, and the base plate is connected to the negative. The electrical current moves from the base plate to the electrode. The majority of the heat is concentrated in the electrode itself (2/3rds). This concentration of heat is caused by the plate’s electrons hitting the electrode at high-velocity, generating intensified heat in the electrode tip.
Because the electrode tip has a high heat concentration, the deposition rate increases accordingly, reducing penetration and fusion in the base plate. The reverse polarity has the benefit of oxide cleaning and removing the oils and dust on the base plate metals’ surface.
Advantages of DCEP
- Oxide cleaning of the base metals reduces inclusion defects
- High volume depositions rate makes welding faster
- Reduced distortion and residual stress
- The DCEP is suited to thinner metal plates and joining metals with low melting points.
Disadvantages of DCEP
- Due to the concentration of heat, the electrode burns faster
- There are high reinforcement levels if the welder slows the welding process
- DCEP is not suitable for thicker plates for joining high melting point metals.
AC or Alternating Current Polarity
Because the AC polarity alternates the direction of the electrons in a circuit back and forth, sometimes up to 120 times a second, it continually moves from negative to positive. Each time the polarity changes, there is a split second of zero amperage, resulting in an arc that may wander (or extinguish.)
Even though AC polarity has the advantages of both DCEN and DCEP, it is essential to use the correct electrodes for AC use. AC electrodes have a specialized coating that keeps the arc lit; however, the arc will still exhibit more fluctuation and stutter than on DC polarity.
Ac polarity is particularly helpful in instances of arc blow due to the magnetism of the base metal. The alternating current enables a steadier arc when welding magnetic parts or unsteady arcs in windy conditions.
AC Polarity Advantages
- AC supports higher temperatures during welding
- AC performs oxide cleaning similar to DCEN
- Allows deeper penetration than DCEP
- Allows a steady weld on magnetized materials.
AC Polarity Disadvantages
- The AC does not support the equally smooth welding arc similar to DCEN and DCEP
- AC welding has higher splatter levels
- The arc may be unreliable and more difficult to control
How do You Select The Correct Polarity?
- If your base metal is magnesium or aluminum, then DCEP should be chosen because of its oxide cleaning capacities.
- If your base metal is Stainless steel, DCEN gives a smooth flow and good penetration.
- Thicker base plates benefit from DCEN due to its good bead profile and penetration.
- Thin Plates are best with the DCEP polarity due to its high deposition rate and more shallow penetration and reduces the chance of burn through.
How does polarity affect arc welding performance?
Polarity is an essential factor behind the creation of a good quality welded joint. Polarity is dependent on your fillers, electrode type as well as chosen base metals. Weld polarity affects parameters such as:
- Deposition Rate. Your filler deposition rate increases when you utilize consumable electrodes using the DCEP polarity
- Weld Penetration. When you chose the DCEN polarity, you will increase your weld penetration.
- Reinforcement. The DCEP polarity increases the weld bead width by increased globular metal transfer.
- HAZ or Heat Affected Zone. Because DCEN concentrates a large proportion of heat in the base plate itself, your HAZ area becomes wider.
- Oxide Cleaning. DCEP is your best option when using plates with dirt or imperfections on the surface area by performing oxide cleaning actions. This cleaning capacity reduces your chance of inclusion defects.
Frequently Asked Questions
You can easily ascertain which welding rod is suited for in the code itself.
The first two numbers represent the psi that the resulting weld can withstand, so multiply the 70 by 1000 gives you 70,000 lbs of pressure per square inch
The third number tells you the position the rod may be used:
1-Means all positions
2-Flat/horizontal
3-Overhead or vertically up or down.
The last number, 8, signifies that it is low hydrogen potassium and iron powder and is suited to AC, DCEP, and DCEN
So the 7018 welding rod may be used in DCEP for thinner plates and DCEN for thicker welding plates.
Although stick welding aluminum is not a preferred way because it is really difficult to lay adequate beads, it can be done with DCEP.
Typically welders would use the AC polarity when the metals they are working on are magnetized. AC is also useful when welders seek prettier beads with a little less penetration than DCEN provides.
Conclusion
Understanding polarity in the welding process is essential in mastering the art of a proper weld. Each polarity has its benefits and drawbacks, and ultimately, the correct choice is dependent on what material you are using your fillers, and your machine type. Once your polarity is correct, you will find your welds will improve considerably.