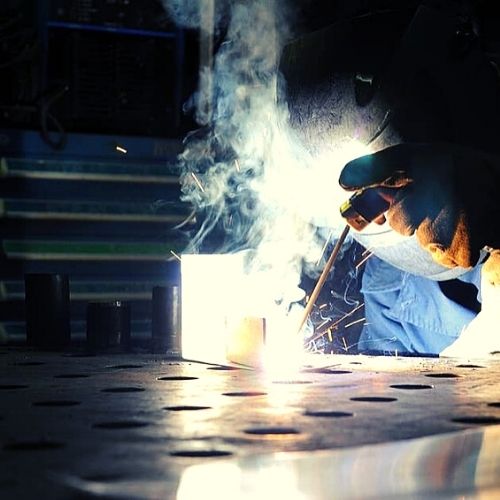
There are a lot of websites on the internet that will convince you to buy a MIG or a TIG welder stating simply that some of the welding techniques cannot be used with a stick welder. The truth is a little different from that, it is true that stick welding is not the preferred choice for welding aluminum, but it can be used for that. So, before you go ahead to buy an expensive new machine for aluminum welding be sure to go through all the information available related to it.
Aluminum can be welded using stick welding but it is not recommended to do so. MIG or TIG would be a better option in terms of the output but nevertheless, it can be done. Keep in mind a few things, first: clean the base metal, pre-heat it, use aluminum rods, and reverse polarity. Pay close attention to the angle and the arc length you are about to use and the fast travel speed you will need.
CAN YOU WELD ALUMINIUM WITH ARC WELDER
Contents
If you are strictly asking whether welding aluminum with a stick welder is possible or not, the answer is yes but it is hardly recognized as the preferred method. If there is a pecking order for selecting the welding method for aluminum it would go about like this: the best process is considered to be TIG for the highest quality results. The second preference would be MIG especially if the base metal is thicker.
On the other hand, when we talk about stick welding, it is not recognized as the best method, but it can be used for small repairs and can get the job done. There are a few factors that can cause additional difficulties when using stick welding for aluminum. One of the issues is the cost of aluminum electrodes, one pound of them can cost up to 20-30 dollars and a lot of places only sell about 5lb which can make your small repair job quite expensive.
Another factor is the preparation work you have to do before starting the weld. Usually, the electrodes used for welding aluminum are hygroscopic which means that they have an affinity towards water. If you don’t take proper care of the rods and leave them overnight outside, they can get damp and gummy. Then there is also the factor that welding with aluminum welding rods isn’t generally recommended under about 1/8” thickness.
The actual welding process can also get a bit tricky; this process requires you to move with speed as the metal melts rapidly which entails that you need to make a rapid forward motion that requires intense concentration.
CAN YOU WELD ALUMINIUM WITH AC-ONLY STICK WELDER?
Keep in mind that aluminum electrodes are DCEP (Direct Current Electrode Positive) reverse polarity. I haven’t heard of anyone using a different polarity while stick welding so I wouldn’t recommend any other polarity. I haven’t read anywhere that you can weld aluminum with AC only stick welder either. Usually, these DC flux coated electrodes will not work directly with an AC output because the arc can get extinguished during the zero voltage portion of the sine wave.
CHOOSING THE RIGHT ROD FOR THE JOB
You should be careful picking out the electrodes you are going to use while welding aluminum, if not done right, you might get some lackluster results. A lot of people recommend the 4043 electrodes for the job. Also keep in mind that when using aluminum rods, the flux will likely spatter all over the place. And when it is cooling it might adopt a muck-like appearance. So don’t get alarmed if this is your first time observing something like this.
Different types of alloys will result in different variations and the sticks you end up using. So you might not face this experience with the types of stick you end up using. But it is important to know and be ready for the risks and quirks of the process ahead of time.
PICKING THE SETTINGS TO WELD ALUMINIUM
The key to welding aluminum is to use a more powerful, direct current welder and a right electrode. You should also be careful about cleaning the base metal of any oxides or solvent oils and pre-heating the base metal before starting your work. The rest of the settings depend on the electrode you are choosing. Taking the example of MG 405 aluminum rods which are compatible with most grades of aluminum, the recommended amperage settings provided by the manufacturer are about 50-80 amps for 3/32” rods, 80-130 amps for 1/8” and 100-160 for 5/32”.
SHOULD YOU PREHEAT THE BASE METALS?
Most people will recommend you to heat the metal before starting the work, pre-heating the metal will allow for a smoother welding experience. Let’s take a look at how to get it done.
Before you start your weld you can heat the aluminum to make it a bit cleaner by directly applying heat to the metal using a torch with a carburizing flame. When you do this, it will result in the formation of soot on the surface of the metal. After the first step switch, back to a neutral flame and concentrate the heat on the aluminum. A good sign to know when the heating process is done is to wait for the soot to clear. This is a rough indication that the metal has reached about 400 degrees F.
ALUMINIUM WELDING TECHNIQUES
Once you have heated your base metal we can move on with the next steps to continue. Keep a few things in mind before you start welding, the oxide layer covering aluminum can be removed in multiple ways. The first and probably the best results can be achieved by using a stainless steel wire brush. You can also try filing the metal by sanding applying light pressure, or chemical etching, but the first method is probably the best and easiest.
Don’t try to use the grinding wheel which you have been using for carbon steel as the results will be quite opposite then what was intended. It will end up folding the oxide layer into the metal.
The recommended angle for welding aluminum is at an angle point straight toward the desired endpoint (not from an upward, downward, or another angle). This type of welding will also require you to move fast as I mentioned before while also maintaining a short arc. Always keep these things in mind while working with aluminum.
The overall process for stick welding aluminum is quite similar to that of other metals but keep the above points in mind. one more thing that will make life easier for you is to expose a tip of the electrode to make the starting process a bit easier.
WHY IS WELDING ALUMINIUM SO DIFFICULT
Before we learn about which techniques are best for aluminum it is important to understand why this metal has such an allure to it. What are the factors which make welding aluminum tricky?
- One of the areas which pose difficulty is the filler metals. there are some aluminum alloys that cannot be welded without curtain rods. For example welding, a 6061 with a 6061 filler metal will result in weld failure.
- Another issue that arises is its higher thermal conductivity when compared to steel. The heat is dispersed more rapidly when the welding is initiated as compared to welding an iron-based alloy. This results in full penetration being delayed until the weld has progressed quite far from the start.
- One more problem created by this thermal conductivity is the formation of larger craters. This is because, by the end of the weld, the heat being created is much higher than in the beginning. The heat is dispersed well in aluminum and can result in larger craters. This might also result in crater cracking which aluminum is very susceptible to. Therefore, the craters should be filled in so that failure does not occur in the future.
- Aluminum also requires specific pre and post-weld processing. This is because of the formation of an oxide layer that has a higher melting temperature than the actual metal itself, this can result in the presence of un-melted aluminum oxide particles in the weld. To avoid this, special oxide removing processes are in place. Some of these include wire brushing or chemical cleaning, these should be used before the start of the weld.
- Sometimes post welding aging is required as the heat from the weld ruins the benefits gained by artificial aging. Some alloys such as 6061-T6 are artificially aged to increase their strength. Heat affected zones result in large reductions in strength.
SHOULD YOU WELD THIN ALUMINIUM WITH STICK?
I could not find a straight-up yes or no answer to the question. Stick welding is anyways difficult when working on thin metal sheets and aluminum is further complicated on top of that. the electrode example I took before has the thinnest electrode at about 2.4mm or 3/32 thickness so I would not recommend using stick welding on anything less than a quarter inch. If you are going to use stick welding for thin sheets, I would recommend asking an expert about the specific details regarding it.
CAN YOU WELD ALUMINIUM TO STEEL?
the answer to this question is not a straight-up yes or no. either the truth is that it is complicated. First, let’s look at why there is a problem in welding both the metals together. Aluminum and Steel have different metallurgy and melting temperatures. For example, carbon steel has a melting temperature of 2500 degrees Fahrenheit while aluminum melts at 1218 degrees Fahrenheit. If you are to use arc welding here, aluminum would be liquefied by the time steel begins to melt. Stick welding would also result in a brittle compound and would not create a strong fusion.
Another reason for this difficulty is the difference in thermal expansion of both the metals. Aluminum will end up expanding almost twice as much when compared to steel as it heats up. The welding may crack under the strain when the metal cools off.
DOES WELDING ALUMINUM WEAKEN IT?
If you take a look at the data provided by ESAB about aluminum alloy yield strengths before and after welding there is an average drop of about 50% but that is the worst-case scenario. Take the example of 6061-T6 grade aluminum which has a yield of a base alloy of about 40ksi, and when welded results in a yield of about 18ksi which is a drop of 55%.
There is a way of tackling this issue and it’s by using another method with other filler material during the welding process. For different grades of the metal, you need to use a filler that will maximize the strength of the weld.
BETTER ALTERNATIVES TO BOND TWO PIECES OF ALUMINIUM
- Stick welding is not the preferred choice when it comes to welding aluminum, one of the most popular methods is the GTAW or TIG welding (Gas Tungsten Arc Welding). One of the advantages of using TIG welding is that it does not require mechanical wire feeding, which can sometimes create findability issues. Instead, the filler material is fed into the puddle by hand. Another advantage of using this process is the cleanliness and neat look after the job is done.
- Gas Metal Arc Welding (GMAW) or MIG welding is also a popular choice for welding aluminum. It has the advantage over TIG of faster traveling and higher depositions rates but at the same time, it uses a mechanical wire feeding system. This requires a spool gun to make aluminum wire feeding possible. Another thing to keep in the mind is to not use 100% CO2 or 75% argon/25% CO2 shielding gas. These gases can be used for steel but not for aluminum as it cannot handle the reactive Co2 gas.
FREQUENTLY ASKED QUESTIONS:
This is one of those topics which a lot of people at first glance just shrug off because of the obvious better alternatives of using other methods. But a lot of people don’t have the option of buying another welder just so they can work on aluminum alloys occasionally, it would be much more economically feasible for a lot of people to just use stick welding even if the results are not the best. This topic is also a bit complicated, there is not a lot of concrete information out there about how to exactly go about it, and a lot of it is hearsay at best. It is common for people to have a lot of questions about this topic and I will try my best to tackle a few of the most popular ones.
It’s not just aluminum but welding a lot of metals generally makes them weaker when compared to the base metal if steps are not taken to correct them. So yes, welding aluminum generally weakens it and for a number of reasons. The main reason being that heat affects the temper of the metal which can result in a loss in yield strength.
It is recommend to use reverse polarity (DCEP) when stick welding, although I am not sure about what the result would be if it was not done so.
Brazing can produce as strong a joint as welding. Brazing is a technique that has become quite popular in recent times because of some of the advantages it has over welding such as low cost of entry in terms of economics and skill level and the smooth and quick process it delivers. Brazed joints can be as strong as the base alloys being used if done correctly.
CONCLUSION
To sum it all up, aluminum can be welded using stick welding but it is not recommended to do so, MIG or TIG would be a better option in terms of the output but nevertheless, it can be done.
Some things to keep in mind:
- don’t forget to pre-heat it before welding.
- use aluminum electrodes
- use reverse polarity
- keep the right angle
- pay attention to the arc length and the fast travel speed you will need.