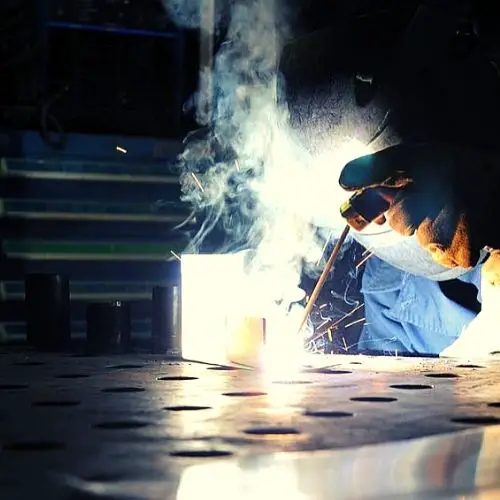
When you are just starting out, this is one of those things which is bound to happen. But you don’t have to stress about it, it happens with the best of us. There are a lot of reasons why your welding rod may stick to the metal but the chances of it happening get reduced a lot if you keep a few things in mind. I remember when I started welding. I faced this exact situation a lot of times, and usually, it could have been avoided if I was more careful.
Let’s take a look at the Do’s and Don’ts and how to avoid this situation.
Among all the reasons why your welding rod is sticking to the metal, the most common one would be low amperage values. Other reasons include flux problems and a lot of times it can be due to simply using the wrong welding technique or electrode size.
One interesting fact related to this problem is the origin of the name ‘stick’ welding. Now, I am not sure about this as a fact, but a lot of people believe that the origin of Shielded Metal Arc Welding, also known as SMAW or ‘stick’ welding comes from the fact that a lot of beginners end up sticking the electrode to the base metal.
WHY DOES MY WELDING ROD KEEP STICKING
Contents
I am pretty sure you know the frustrating feeling of trying to pull off the perfect weld but ruining it because of your rod sticking to the metal.
Let’s look at a few reasons why this must be happening.
Low settings
One of the most common reasons for the rods to stick to the metal is the low amperage or the current value is used. What this means is that the current is enough so that the tip of the electrode can melt but not enough to properly strike an arc. If the flow of the current is not sufficient then the rod will not dissolve properly and therefore, it will stick to the base metal.
Unstable current
The other reason is the low or unstable open-circuit voltage. If the current flow is not stable, the chances of the electrode sticking with the metal increase exponentially. What happens is that if your OCV (Open Circuit Voltage) is unstable or too low it can become very difficult to strike a proper arc. When it is low, the arc can keep disappearing and when you attempt to strike an arc again the electrode is very likely to stick.
One of the reasons for the low OCV can be the high resistance between the ground and the workpiece. So, make sure that this is not one of the problems.
For additional reading: Can a welder shock you while welding
Too short arc
This upcoming reason is one of the most common ones made by newcomers as this is also one of the most important factors when it comes to welding, and that is the arc length. For people who don’t know what this exactly means, the arc length is basically the distance of your electrode to the base metal. In other words, it’s the length of the electric arc.
There are two scenarios, one, where you take the electrode too far from the base metal in which case the arc will disappear. Second, when you bring the rod too close to the base metal in which case the rod will end up sticking to the base metal. That’s why it gets very important to maintain a proper arc length.
Dirty surfaces
Remember when I talked about increased resistance? Well, your base metal being dirty can also be a reason for this increase. If your voltage remains constant, then the current can vary depending on the resistance, and having rust or dust on the metal can increase the resistance. With this increase, striking an arc can become tough and even if you do it, the rod can keep sticking to the metal.
Using the wrong electrode
Have people told you that its important to choose your electrode carefully? Well one of the reasons for that advice is the rod sticking issues. Even if you are using the right current and voltage and your base metal is clean, your rod can keep sticking. This can become very frustrating when things keep going wrong and you don’t know why. Incorrect electrode selection might be one of the issues.
Some rods only work for DC and some work both for DC and AC, I am sure you know about this. But if you use a thick rod on thin metal sheets, the rods can keep sticking because of striking issues. For example, if you are using the 5/64” 6013 and it keeps on sticking, try switching to a 1/16”, it might solve the issue. This issue can be a bit tricky to get hang of if you are just starting in the world of welding.
WHAT TO DO WHEN THE ROD GETS STUCK TO THE BASE METAL
Most of the readers must be coming to this article because this incident has already happened to you or that you are worried it might happen to you. You don’t need to worry about this a lot. A lot of professional welders also get their electrodes stuck to the metal. Usually, it can be easily fixed and should not be a big deal.
The first thing you should try to do is to give it a nice jerk, something as simple as this might set it free. But on the other hand, your electrode might get tightly glued to the metal, if this happens you have two options:
- shut your welder off before trying to remove it. At this stage the only thing you can do is to break off the rod from the metal, the tip of the electrode which includes the flux might fall off, but you don’t need to worry too much about it.
- Remove the welding stinger from the electrode as fast as you can, turn off the welder and break off the rod from the metal.
One thing to keep in mind about this rod is to not use it directly again on the metal. If the flux has fallen off, then the bare metal of the rod will most likely get stuck to the base metal again. In this case, what you should do is to try to cut off the rod to the point where the flux has fallen off.
HOW DO YOU STOP WELDING ROD FROM STICKING
A lot of these tips and tricks will largely relate to the issues which cause the rod to get stuck on the metal in the first place. It is not enough knowing what the problem is if you don’t know what to after finding it out. I hope this part will help you with diagnosing and treating the problem.
Choose the right settings
The first problem which you should take care of is choosing the proper amperage settings. Don’t forget that different electrodes you use will require a different amperage setting, you should properly research this before starting your weld. Usually the 6010, 6011, 6012, 6013 will require a lower amperage value as compared to the 7018 and 7014.
There are a lot of amperage value charts out there that can give you a decent enough idea about what amperage to use with what electrode.
Pick the right size rod
One more thing to keep in mind is the variation of amperage requirements with the thickness of the rods. The thicker the rod, the higher the current it needs to melt. Also, pay heed to the resistance of the circuit as a whole also, you might need to increase the current by a little if the overall resistance is too high. By the way, if the tip of the rod starts glowing, it is a good indication of the current being too high. Always try to refer to the manufacturer’s recommendation.
Check the condition of the rods
The other recommendation I can give is to make sure your electrodes are in good shape. By that I mean two things, one that the electrode itself is of good quality. The other is to make sure that your electrode is not degraded or rusty. You can check the condition of your electrode by trying to rub off the flux with your fingers, if they fall or break off it is a good sign to change the rod. These poor-quality rods are more likely to stick and also, they might be dangerous to work with.
Make sure that your rods are not covered with dust, rust, moisture, oil, or any other contaminants.
Check the ground connection
The next point a lot of people including veterans often overlook. That is to keep a good ground connection. Even if you think your ground connection is perfect there can be that one wire which has developed cracks that you haven’t noticed. If rust has developed over your terminal connection, try to cut off the wires and make fresh joints. If the ground connection is faulty, it can both dangerous for you and increase the overall resistance of the circuit, making the amperage requirement higher.
Practice striking an arc
Make sure to practice your arc striking skill as well. it takes a lot of people weeks and months to practice and perfect this technique. There are usually two ways to strike an arc, the dragging method, and the tapping method.
Coming back to the arc length, this technique goes along with the arc striking. Perfecting these takes a lot of practice is the most common reason for the rods sticking to the metal. One good rule is to never exceed the arc length higher than the diameter of the metal core of the rod.
Also, try to keep the travel speed and the angle constant, too much variation not only provides a bad quality weld. it can also make your electrode stick to the metal. And once your electrode is stuck, it can be difficult to bring the flow of the weld back.
SOME TIPS FOR STRIKING AN ARC
Throughout this article, you must have heard me saying that striking your arc and maintaining the proper arc length is very important. This advice wouldn’t help you too much if I didn’t give you some tips about them. I hope these tips will help you improve your technique and not only that, improving your technique will save you a lot of time and electrodes.
There are majorly two methods of striking an arc, the tapping method and the scratch start method (also known as the dragging method). It is probably better for you to learn the latter first if you are a beginner. The first method has a higher chance of your rod getting stuck.
Some of the steps which you should keep in mind:
- The first thing would be to decide the direction of the weld and choosing the starting point.
- Before striking an arc hold the rod about an inch above the base metal and tilt it in the direction of the weld.
- To strike an arc, don’t poke at the metal but try softly scraping the surface. Imagine lighting a match. As soon as you see an arc, move back to the original location.
- If you have been unable to strike an arc after a few tries, it is better to change the electrode as it will cause to build up material at the tip. Don’t throw this rod away, you can scrape the build-up off once it cools down.
- Use small diameter rods as a beginner.
WHAT IS THE EASIEST WELDING ROD TO USE
In my opinion, one of the easiest electrodes to use for a beginner is the 6013, 7014, even the 7018 is pretty easy to use but the handling problems associated with it makes it not suitable for beginners. Thicker electrodes are more likely to stick as I mentioned before, so try sticking with a thinner one in the beginning.
FREQUENTLY ASKED QUESTIONS
It is perfectly normal for you to have a lot of questions after going through the article, I wish I had access to such a community while I was learning about the basics. It is better to clear every doubt you have for your safety and the quality of the weld as well.
Dirty surfaces can make it harder to strike and maintain an arc with the base metal. There is also the added effect of increased resistance of the circuit which can require more amperage than the settings you are welding on. Remember Ohm’s law? It’s the same principle here.
The easiest and safest method for you to take is to go by the manufacturer’s guidelines for a particular electrode. If you buy your electrodes from a decent enough company, the manufacturer usually provides you with the recommended amperage settings you should use with the electrode. You can also check some charts available online as a guideline to go by.
As I mentioned above, the easiest thing for you to do would be to try yanking the electrode off the metal. In case the bond is stronger between the metal and the electrode, remove the stinger right away or shut the welder off and try breaking the rod off of the base metal.
CONCLUSION
To sum it all up, make sure that you are choosing the right amperage and the right electrode for the job you have at hand. Also, make sure that the base metal and the rod are clean and don’t have any impurities on them. Keep in mind to check the ground connection of the circuit as well. This is one of the most intimidating and scary situations any beginner can face during the start of their welding journey. Hopefully, after reading this article you will have more confidence while facing these situations.
Always remember to keep practicing.
Recommended reading: