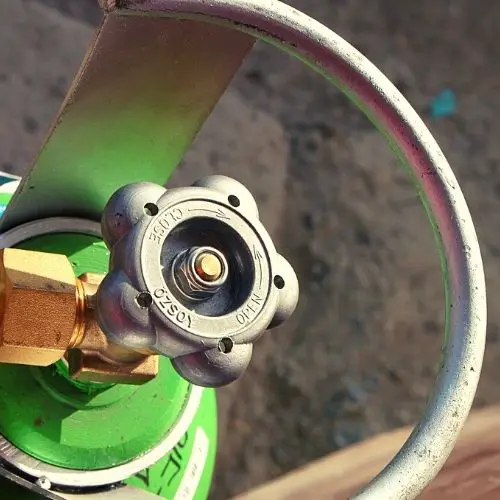
When you are learning a new technique, it is very important for you to learn each and every aspect of it. This is the only way to make sure you actually become good at it. The gas flow rate is one of those things which is often overlooked by a lot of people while it can significantly affect the quality of the weld. This is one of those concepts which is not considered to be fun to learn about, but in reality, it is extremely important to get right. Let’s take a look at the basics of the topic.
So what is the correct gas flow rate for welding? The correct gas flow rate in MIG welding ranges between 15 to 25 CFH. But Make sure to take into account the different variables while selecting the flow rate. Also, take into account the suggested gas flow rates for metals like aluminum or stainless steel which also have a specific gas they should be used with.
GAS FLOW RATE IN MIG WELDING – WHY IT IS IMPORTANT?
Contents
To begin with, the gas flow rate is represented in cubic feet per hour (CFH) and it represents the rate of flow of shielding gas during the welding process, I know it is pretty self-explanatory but if felt I should address it anyways.
If you have decided which shielding gas to use the next step is to decide the correct flow rate for the job. The reason why this step is important is so that the molten metal pool is properly protected during the weld and smooth welding is achieved on the job. If the gas flow rate is not sufficient it can lead to a bad case of atmospheric contamination. The final weld can result in porosity or oxidation.
THINGS TO KEEP IN MIND WHILE DETERMING THE CORRECT THE GAS FLOW RATE
You will have to take into account quite a few factors while selecting the gas flow rate including the size or diameter of the gas shroud, the travel speed, wire feeding speed, and the amount of mill scale on the base metal.
Shroud diameter (in mm) | 6 | 8 | 10 | 11 | 13 | 16 |
Shroud diameter in inches | 1/4 | 5/16 | 3/8 | 7/16 | 1/2 | 5/8 |
Flow rate (CFH) | 10-14 | 11-15 | 12-16 | 13-17 | 17-20 | 17-20 |
Flow rate (litres per minute) | 5-7 | 5-7 | 5.5-7-5 | 6-8 | 8-9 | 8-9 |
One way to know if the gas flow rate is too high is if the gas flow is turbulent during welding and this can result in porosity in the final weld.
Even an increase in the speed of feeding the wire can result in a need to increase the flow of gas rate as an increase in wire feeding speed can increase the size of the weld profile as well and you will need more gas to cover the welding area.
You need to make sure that the nozzle size is appropriate for the job. Sometimes when there is too much spatter while welding it can block the nozzle a little bit and it can lower the flow rate.
You should always make sure that the equipment you are going to be using is properly maintained and in good condition.
The final thing on which the flow rate depends upon is the type of gas and material being used, if you are using an argon based gas you will need a higher flow rate. This is because argon is heavier than air. on the other hand, if you are going to be using helium-based gas then you will need a lower flow rate.
The flow rate will also be directly proportional to the thickness of the material. If the materials are anywhere between 1-3 mm in thickness then a relatively lower flow rate is required while if the materials are thicker than that it can go up.
FLOW RATE FOR ALUMINUM MIG WELDING
Aluminum has an interesting property that requires a specific gas to be used while welding. Aluminum is non-ferrous metal and therefore you should only use 100% argon as the shielding gas. As I said earlier argon requires a higher flow rate and the recommended flow rate to be used on aluminum is 20 to 30CFH.
GAS FLOW RATE FOR MIG WELDING STAINLESS STEEL
Although the gas flow rate will depend on a lot of factors as I have explained before, the preferred range for working on stainless steel is around 20 to 25 CFH. This is keeping in mind if the gas which has been selected is composed of helium mixed with a little bit of CO2 and 20% argon.
HOW LONG WILL MY SHIELDING GAS BOTTLE LAST
The answer to this question depends on a lot of factors. The first thing being how long will you weld for? The second factor being the average gas flow rate you are going to be using.
For the sake of simplicity, I will take the most common numbers being used in the business. Let’s assume that you are going to be setting up the flow rate between 10-20CFH and the size of your bottle is around 250CF, then it should last you for about 10-20 hours. Of course, this assumes that you will be welding non-stop but when it comes to actual practical usage, one bottle should last you quite a bit.
DIFFERENT OPTIONS FOR REGULATING THE GAS FLOW
as the name suggests a regulator is basically used to control and monitor the gas flow rate in the system. They can be divided into two broad categories, fixed pressure/variable orifice and variable pressure/fixed orifice.
The usual flowmeter comes into the former category of fixed pressure system. What this means is that the factory sets up the pressure and the flow can be controlled through an orifice.
Flow gauge on the other hand falls in the other category. A specially drilled orifice is usually used to vary the pressure.
I have a whole article about flow meters and gas regulators here.
FREQUENTLY ASKED QUESTIONS
Choosing the right flow rate has a lot of moving parts involved taking into account the different factors affecting the change in flow rate. It can take a lot of time for people to get choosing the flow rate right. This is the reason why you should be clear about any doubts that you may have. Let’s take a look at the most common queries that people have about this topic.
This step of welding is carried out by the welding gun, which consists of the diffuser, nozzle, and a contact tip. This is the reason why you should ensure all of these components are working properly. The diffuser or the nozzle can get clogged or can be too narrow for some required flow rates which you should be aware of.
When it comes to selecting the right shielding gas, you will have to take into account factors such as the type of metal being worked on and other factors like the cost, etc. The most common and the cheapest shielding gas being used all over the world is CO2.
One easy way to look for any gas leakage either in the gun or the pipe is to use light soapy water, apply it to the point where you think there is a leakage, and if bubbles being formed then you know where the leakage is.
CONCLUSION
To sum it all up, it is as vital to set up the gas flow rate as selecting the electrode for stick welding or selecting the shielding gas in MIG. A bad flow rate can lead to porosity in the final weld. The correct flow rate depends on a lot of factors, some of them being the size of the weld, the travel speed, the wire feeding speed, the type of gas being used, and the base metal you will be working with. Make sure to use the right equipment and try to ensure that the nozzle hasn’t been blocked. Also, make sure you are stocked up on shielding gases if you are planning to weld for a long time.