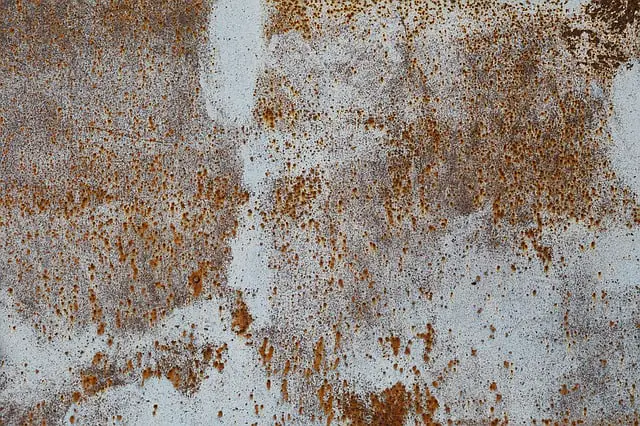
If you are just starting with MIG welding, it can be quite tough to weld delicate materials, so at first, better start welding thicker metals that give you more room for error. When it comes to welding thin sheet metal like car body panels, if you are not experienced and skilled enough, then you can easily create a mess as blow holes in the sheet and make the metal useless. In this article, we are taking a look at how people should go about welding sheet metal, what kind of wire and shielding gas need to be used along with some tips and tricks.
Main Things to Know Before You Start Tacking Sheet Metal
Contents
When welding sheet metal, the main thing to look out is to prevent warping and burn-through. Even professional welders can create excessive heat affected zones and burn through while welding sheet metal. It requires a lot of experience, patience and skill to get the desired results.
For MIG welding sheet metal, it is often recommended to use an electrode wire of the smallest diameter to prevent burn-through and warping. The main reason to use a smaller diameter wire is that it takes less heat for melting and hence the metal around the weld is not heated to a very great extent. This enables you to take control over the welding process along with some chances to recover quickly from any mistakes during the process. The deposition rate is also much lower when compared with using larger diameter wires. Professionals always recommend using a wire of .023 inches diameter for welding very thin metal. This is the one I am using, and it is available on Amazon.
If you don’t weld sheet metal very often then you can probably get things done with .030″ wire as well. No need to buy an extra spool of wire for a small job, but I would still recommend you to check out the Ine welding wire I mentioned in the last paragraph.
According to the American Welding Society (AWS), if you are welding mild steel, it is better to choose E70 series wire with S-2, S-3 classification. And when it comes to shielding gas, you can go for 75% argon and 25% CO2 because argon produces less heat and also helps to reduce the amount of spatter produced.
Aluminum preparation
Before welding, it is extremely important to clean the metals and especially aluminum. Make sure to remove any kind of dirt and oil from the metal using some solvent or a degreaser. You may even use some stainless-steel wire brush or some chemical oxide cleaner to remove all impurities and dirt before welding to get the desired results. Because when welding aluminum, when it comes exposed to the air, an oxide layer is created over aluminum leading to bad weld quality.
If you are interested in stick welding aluminum read this as well.
MIG welder settings for sheet metal
When MIG welding sheet metal, it is important to set the proper parameters to prevent warping and burn-through or else it will create excess heat and easily blowholes on the metal. Keep in mind, during the welding process, it is important to direct the arc right at the center of the weld puddle and don’t do movements like whipping or weaving as it may cause warping and burn-through quickly. Always follow the straight-line method and move quickly from one end to the other to maintain a better-looking bead profile.
Skip welding
To prevent warping and distorting while welding sheet metal, it is important to have an even distribution of heat. Generally, the skip-welding technique is the best way to distribute heat in an even manner.
Say if you are welding an 18 gauge stainless steel sheet that is 2×2 feet in size to repair the side of your tank, start by creating a weld that is 1inch long, then skip 6 inches and then create a 1 inch long weld. Continue the same way along the sides of the piece of sheet metal. This kind of welding is also called as 1 inch-6 inch weld or skip welding as you are skipping some portion of the sheet steel before making the next weld. Now once you completed it till the end, start from the first weld and create a 1-inch weld, 3 inches from the first weld and continue to do so repeatedly until you reach the end. This ensures that the heat is distributed evenly on the metal and helps in preventing warping and distortion.
If You are into stick welding, I also have a post about stick welding stainless here.
Backing bars
In order to dissipate the heat from the welded portion of the metal quickly, try placing the metal with the hotter portion close enough to a backing bar. The backing bar is used commonly by welders to cool the welded metals and they are generally made up of a copper or aluminum metal and clamped to the base of the weld piece whether it is just a piece of thin sheet metal or a body panel, you can use it either way.
If you are welding on a project that needs a higher duty-cycle, it is better to go for a water-cooled backing bar as it will dissipate the heat more quickly and for longer periods. It is nothing but a water cooler that ensures cold water is circulated into the backing bar through the holes drilled into the bar.
Fit-up and joint design
When you are welding thin metal, the pieces need to be tightly fitted to get the desired results. If there are gaps, then during the welding, it possibly will not join the metal sheets properly, it also helps to prevent blowing holes in the base metals, so always measure a couple of times before you start cutting.
Tips for Welding Sheet Metal and Body Panels with MIG
- Better choose a MIG welding machine that comes with infinite adjustability as it will enable you to adjust like the way you wanted. This also helps you in voltage adjustments and the wire feed can be set to any kind of configuration. With machines having infinite adjustability, you can weld sheet metals more easily and quickly.
- It is just the experience that can help you succeed in MIG welding sheet metal without any issues. Hence you need to practice a lot, try out the various setting to find the best setting that works for you. Try welding with a scrap sheet metal piece and practice many times until you start working on more important projects.
- Make sure to use an electrode wire that is thinner as it uses lesser heat and prevents blowing holes on to the sheet metal. Try going for a wire of .023 inches when welding sheet metal.
For sheet metal, I use INE welding wire and it is just as good as their flux-cored wire, if you want, you can grab one here: https://amzn.to/37BeVJ1 - While wire feed welding sheet metal, go for short bursts of welding instead of a going on a long bead. Short bursts or tacks will help you gain more control and adjust easily.
I hope I answered your question on How to weld sheet metal and how to weld sheet metal without warping.
If you have any questions, thoughts comment below!