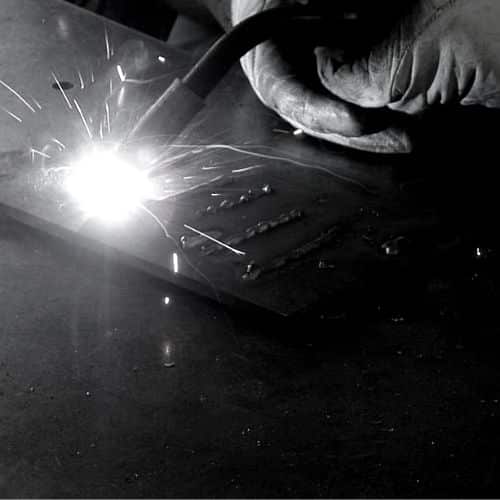
When it comes to the metal fabrication process, welding is one of the most effective methods to bond materials. Welding is a process in which two or more thermoplastics or metal pieces are joined together using pressure and/or heat.
Today, there are different types of welding and one of the most common options is the Gas Metal Arc Welding (GMAW) or Metal Insert Gas Welding (MIG).
GMAW is known as one of the easiest and simplest wedding processes that you can do. In fact, the whole process is simple since it is so easy to control because you only need to operate one element- the welding gun.
However, always remember that even when working with the simplest tool you will have some problems. One of the common problems that you may encounter in this process is that the MIG welder not arcing.
Having enough knowledge about basic MIG welding troubleshooting methods can help you in finding the right answer to the issue and continue with your task.
To help you, in this article, we will look at some of the common problems why your MIG welder won’t arc as well as some easy solutions to the problems.
Bad Ground Clamp
Contents
The first and most common problem why usually MIG welder doesn’t make an arc is that the ground clamp is not attached to the base metal properly. Even experienced welders forget to attach the ground clamp to the workpiece, and if you think that’s the issue in your case, all you need to do is check the ground clamp whether it is connected properly or not. If not, then make sure to fix it. It might be obvious to some of you, but it is important to note that the ground clamp must be connected on a clean surface. If you try to get a good connection while welding heavy rusty plates then most likely you will not get a spark out of your welder.
In addition, your ground clamp may start to malfunction as time passes by. Most of the time, the wires inside the machine get loose or the ground clamp itself needs a replacement. Make sure that all the wires inside the machine are intact and are not oxidized. If that is the case and you have some mechanical skills, unplug the machine from the power outlet and clean the wires one by one.
Inadequate Power Coming to the MIG Welder
Keep in mind that welder needs the power to work and run. However, if you have poor wirings, then this may cause problems. When using a small MIG welder you must have around 110-volts to 120-volts, (you can check it using a multi-meter). A great idea would be to make sure that you have not blown the fuses. If your fuses are burned down then the two main causes to that would be a short circuit in somewhere in your workshop or you welded for too long on too high settings and your electricity network just couldn’t handle it.
If your wire feed is working, then your fuses are okay!
Another common problem is that you’re running to is small or too long of an extension cord. With this in mind, if you’re using an extension cord make sure that it is not too long to prevent any voltage drop.
On the other hand, a short extension cord that you usually use in lighting up your Christmas lights is not enough to run a 135-amp MIG welder. As a piece of advice, get a nice extension cord with thick wires (rated at 30 amps at least for small welder), as it is more sufficient to run a MIG welder.
This one from Amazon should hold up pretty well.
Messy Weld Surface
Bear in mind that a MIG welder requires clean base metals thus if you are trying to weld on a surface that has oil, zinc, old paint, rust, and other coatings your MIG welder may not start an arc, and even if it does, more than likely you will not get good penetration.
For this reason, we recommend that you clean the surface that you will be welding, using a grinder, sander or at least wire brush to get rid of the coating. After that, you can clean the surface with acetone or just with a clean piece of fabric.
Too Tight Drive Roll Tension
Drive rolls are specially made to smoothly feed the electrode wire from the wire spool trough the gun cable, but if the tension of the drive roll is set too tight, the drive rolls will wear down quicker and it can cause rough wire feeding as well that can result in arc instability.
Little tension, on the other hand, may result in wire slipping. For further instructions on how tight the drive should be, I would refer to the owner’s manual.
For those of you who are too lazy to see the manual, don’t use too much strength when installing the wire. No need to use pliers, just your fingers and it should be tight enough.
Wire Feed Motor is not working
If your MIG welder wire feed motor not working, then it is impossible that you can create a continuous arc after your first spark. A welder that will not feed wire usually has one of the two things causing the issue. First, the tension of wire feed system is too loose. And the second one is that the welding tip is blocked by slag or you have burned the wire into it. For the ladder, just changing the contact tip will do the trick to get the machine up and running again.
A damaged internal motor SHOULDN’T be fixed at home to avoid worsening the problem. Thus, it is best that you let a professional welder repair technician do the job.
To wrap things up, last time I had a similar problem – the machine fed the wire but did not create an arc. I have had loose wiring inside the machine before and also basic knowledge in electricity but I just couldn’t figure out the problem, so I asked a friend who is an electrical engineer to take a look. It turned out that some relay in the control plate had oxidized so badly that it was a miracle that the machine ran just a couple hour earlier.
Luckily all the parts needed were available in a nearby shop, so my friend installed the new relay and few new diodes and in no time I had the machine up and running again.
The whole repair cost about 10 bucks so it was definitely better than buying a new welder.
Conclusion:
I hope this small guide helps you determine the most common problems when your MIG does not create an arc. By arming yourself with this basic information, you will be able to identify possibly the upcoming problems and look for effective solutions more rapidly and maybe even avoid some of them, like buying a great extension cord! Hopefully, you have learned a lot from this article.